Mechanical pressure gauges require no external power and provide a reliable means of accurate pressure measurement. To properly select a pressure gauge you need to consider the following:
1. Accuracy Accuracy is usually defined as a percentage of the full scale range. As a guide the following is often used:
Test gauges: 0.25% to 0.1%
Critical Processes: 0.5%
General Industrial Process: 1.0% accuracy, 2% for less critical
Refer to ASME B40.1-1998 or the DIN specifications for more information on accuracy.
2. Dial Size Dial sizes typically range from 1.1/2" to 16", but the most commonly used sizes are 100mm (4") and 150mm (6") for process gauges and 250mm (10") for test gauges. Generally readability requirements, space limitations and required gauge accuracy determine the dial size.
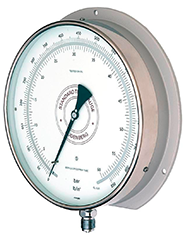 | 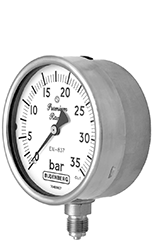 | 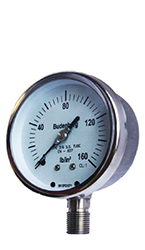 |
---|
10" Gauge | 6" Gauge | 4" Gauge |
ASME B40.1-1998 recommends that the normal operating pressure should be confined to 25% to 75% of the scale. If pulsation is present then the maximum operating gauge pressure should not exceed 50% of the full-scale range. The scale on the gauge is usually printed in either Bar, Psi or dual scale i.e. Bar and Psi. Other units are available and custom scales are possible. Please contact us for further information.
Bar Ranges
-1 to 0 | -0.6 to 0 | 0 to 0.6 | 0 to 1 |
---|
0 to 1.6 | 0 to 2.5 | 0 to 4 | 0 to 6 |
0 to 10 | 0 to 16 | 0 to 25 | 0 to 40 |
0 to 60 | 0 to 100 | 0 to 160 | 0 to 250 |
0 to 400 | 0 to 600 | 0 to 1,000 | 0 to 1,600 |
Psi Ranges -15 to 0 | -10 to 0 | 0 to 10 | 0 to 15 |
---|
0 to 30 | 0 to 60 | 0 to 100 | 0 to 160 |
0 to 200 | 0 to 300 | 0 to 400 | 0 to 600 |
0 to 1,000 | 0 to 1,600 | 0 to 3,000 | 0 to 5,000 |
0 to 6,000 | 0 to 10,000 | 0 to 16,000 | 0 to 20,000 |
4. Case Material & Type The case and bezel selection of a pressure gauge should be in accordance with the gauge environment which will help determine the material and also the safety requirement.
Cases are typically available in ABS Plastic, painted steel, chrome-plated steel, brass, stainless steel, aluminium and phenolic turret.
Cases are available in three types with Type 3 (or S3), offering the user the highest level of user protection should a gauge fail. The Budenberg 736 pressure gauge uses a Type 2 gauge safety case and the Budenberg 966 pressure gauge uses a Type 3 gauge safety case.
5. Process Medium The wetted parts of the pressure gauge, the bourdon tube and socket must be compatible with the process medium. Bourdon tubes are most commonly made from phosphor bronze, 316 stainless steel, or monel. If it is not compatible or the media is extremely viscous or dirty, a diaphragm seal / gauge isolator can be used but it will add an additional error to the reading.
6. Gauge Connection Gauges are available with a variety of connection threads including BSP, NPT, DIN, JIS & SAE. 3/8" and 1/2" are the most commonly used.
7. Pulsation and Vibration Pulsation and vibration will decrease the life of the gauge. In these situations a liquid filled gauge or an internally dampened gauge should be used. Budenberg offer liquid filled gauges as well as a unique method of gauge dampening called Viscous Damped Movement (VDM), that provides the performance of a liquid filled gauge without requiring a liquid fill. Other accessories that minimise the stresses on the bourdon tube / movement include pulsation dampers, pressure snubbers, gauge savers and diaphragm seals but these will all add an additional error to the reading.
8. The Environment Environment considerations include temperature, airborne particulates (particles in the air), condensation, humidity, water and exposure to other chemicals. Temperature can affect the accuracy and integrity of the gauge. Gauges are usually available either temperature compensated or non-temperature compensated. When ambient conditions are corrosive, contain a large number of particulates or maybe exposed to a wet or humid environment including wash-downs or rain, a weatherproof/hermetically sealed or liquid filled gauge should be used.
9. Mounting Requirements Usually available as:
- Direct stem mount - Lower connection
- Wall/Surface Mount - Lower connection
- Panel surface mount - Back connection
- Panel hole U-Clamp flush mount - Back connection
- Panel hole front flange flush mount - Back connection
10. Other Notes If using a gauge on steam then always use a Type 3 (S3) safety gauge.
If you have a system were you are regularly dumping all of the pressure then ideally use a gauge without a rest pin at zero.
If there is a pin at zero then the first 10% is often not covered by the calibration.
Typical gauge life cycles are around 200,000.
Every 10 degC difference to ambient temperature adds approximately 0.4% error to a gauge.
Glossary of Gauge Related Terms - Gauge Pressure: Indicates pressure from a single source and uses ambient pressure as zero.
- Absolute Pressure: The pressure measured above a perfect vacuum. i.e. Absolute Pressure = Gauge Pressure + Atmospheric Pressure
- Differential Pressure: The difference between two independent, but related pressures.
- Compound Pressure Gauges: Indicate pressures above and below ambient pressure - positive and negative pressure.
- Duplex Gauges: Utilises two independent sensing elements each connected to different but related pressure sources.
For further help with these products please contact us on +44 (0)1482 601030 or email
sales@flowstar.co.uk.